To improve housing costs and economic conditions at once, look to the locations of modular housing factories.
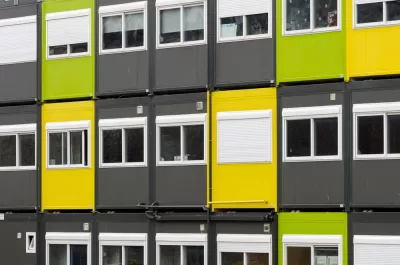
Affordable housing developers are keenly aware of the growing need to house struggling residents quickly. The pandemic has only exacerbated the mismatch between housing supply and housing need. There is, of course, also an economic crisis, and affordable housing development is a proven strategy to spur job creation and spark positive ripple effects across multiple sectors.
However, operational challenges precipitated by the pandemic—not to mention the strain on public resources‚ have made affordable housing developers extremely sensitive to the costs of building new developments. This has increased the appeal of modular housing construction, which has been promoted as a way to boost productivity, cut costs, and force innovation in traditional construction. Modular homes are residences built to near completion in factory environments, and later transported in sections to construction sites.
However, that potential has not yet been realized, and one of the reasons is the expense and delay that comes from shipping the modular parts in from distant factories. If components of a modular home are built at a local factory situated nearer the construction site, developers have the convenience of both logistical and cost efficiencies, cutting down project time and contributing to a smaller carbon footprint.
A strategy that would address housing supply, construction cost, job creation—and even the jobs-housing mismatch—would be to locate more modular housing factories directly in regions with high housing costs, in parts of those regions that suffer from lack of jobs and long commutes to what jobs there are. Developers seek certainty in the building environment, and a robust set of local fabrication facilities could bring efficiency, reliability, and timely delivery.
Take Southern California, for example. The Southern California Association of Governments (SCAG), the metropolitan planning organization for the region, has been told by the state housing department that the region will need ...
FULL STORY: Build Modular Housing Factories Near Areas with High Housing Costs

Maui's Vacation Rental Debate Turns Ugly
Verbal attacks, misinformation campaigns and fistfights plague a high-stakes debate to convert thousands of vacation rentals into long-term housing.
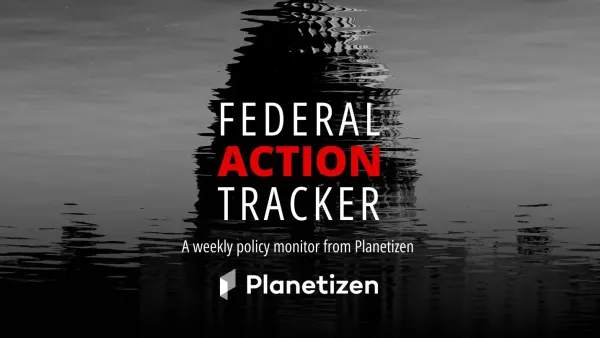
Planetizen Federal Action Tracker
A weekly monitor of how Trump’s orders and actions are impacting planners and planning in America.

In Urban Planning, AI Prompting Could be the New Design Thinking
Creativity has long been key to great urban design. What if we see AI as our new creative partner?

King County Supportive Housing Program Offers Hope for Unhoused Residents
The county is taking a ‘Housing First’ approach that prioritizes getting people into housing, then offering wraparound supportive services.
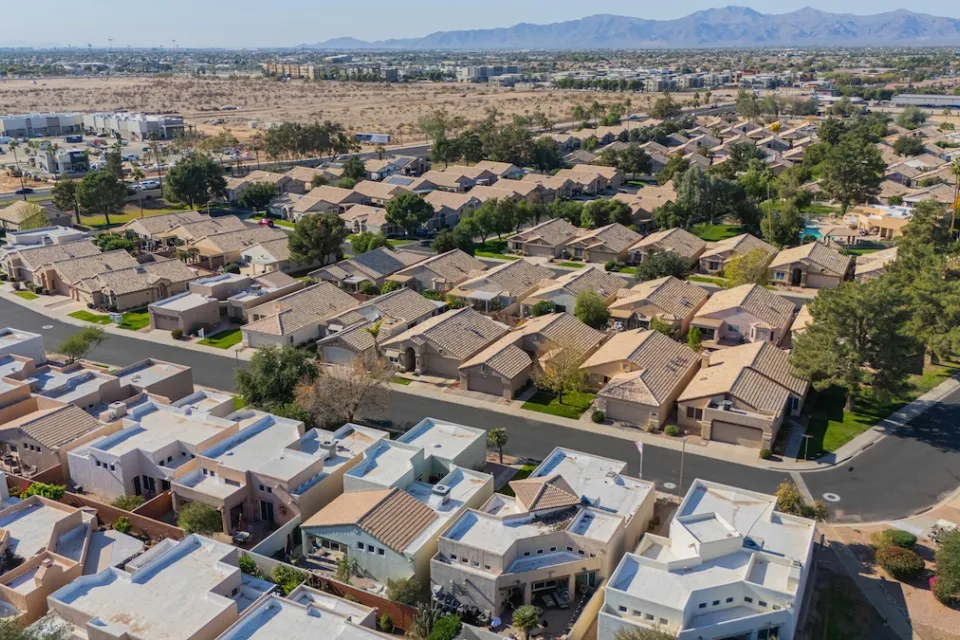
Researchers Use AI to Get Clearer Picture of US Housing
Analysts are using artificial intelligence to supercharge their research by allowing them to comb through data faster. Though these AI tools can be error prone, they save time and housing researchers are optimistic about the future.
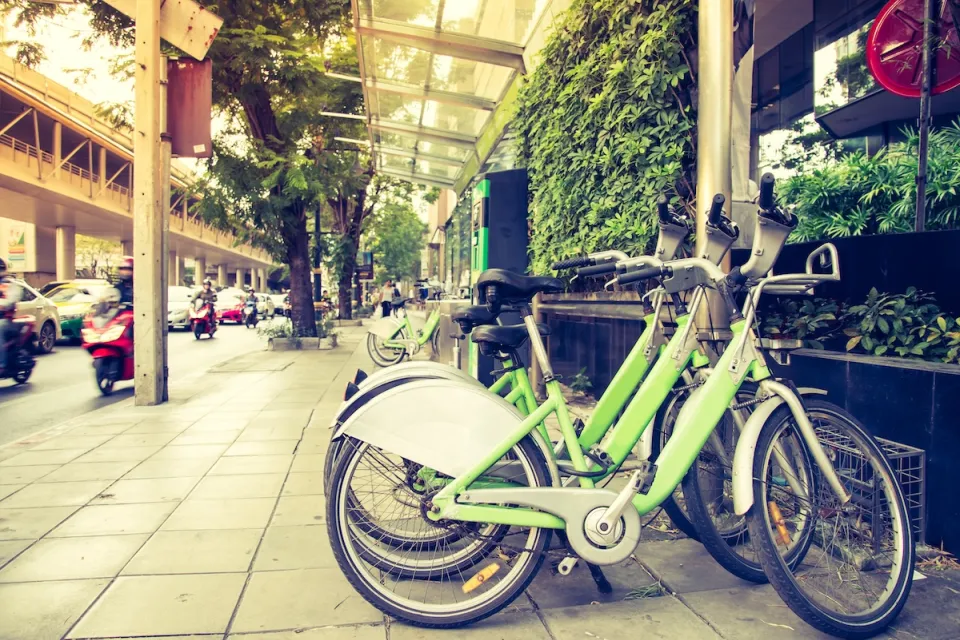
Making Shared Micromobility More Inclusive
Cities and shared mobility system operators can do more to include people with disabilities in planning and operations, per a new report.
Urban Design for Planners 1: Software Tools
This six-course series explores essential urban design concepts using open source software and equips planners with the tools they need to participate fully in the urban design process.
Planning for Universal Design
Learn the tools for implementing Universal Design in planning regulations.
planning NEXT
Appalachian Highlands Housing Partners
Mpact (founded as Rail~Volution)
City of Camden Redevelopment Agency
City of Astoria
City of Portland
City of Laramie